You’ll often face issues like drive motor failures, alignment problems, and mechanical wear, so regular inspections and specialized troubleshooting tools are key. Supply chain disruptions can delay parts, so building good relationships with suppliers helps. Maintaining charging infrastructure and battery systems with proper protocols minimizes downtime. Ensuring your team has ongoing training improves repairs and reliability. For a deeper look into tackling these common challenges effectively, continue exploring proven solutions and best practices.
Key Takeaways
- Regularly inspect and maintain drive motors and alignment to prevent handling issues and costly repairs.
- Ensure availability of quality spare parts and establish reliable supply chains to minimize downtime.
- Perform routine checks and proper procedures for charging systems and batteries to extend lifespan and prevent failures.
- Invest in specialized training and diagnostic tools for technicians to efficiently troubleshoot electrical and mechanical faults.
- Upgrade infrastructure and standardize charging systems to improve operational reliability and reduce maintenance complexity.
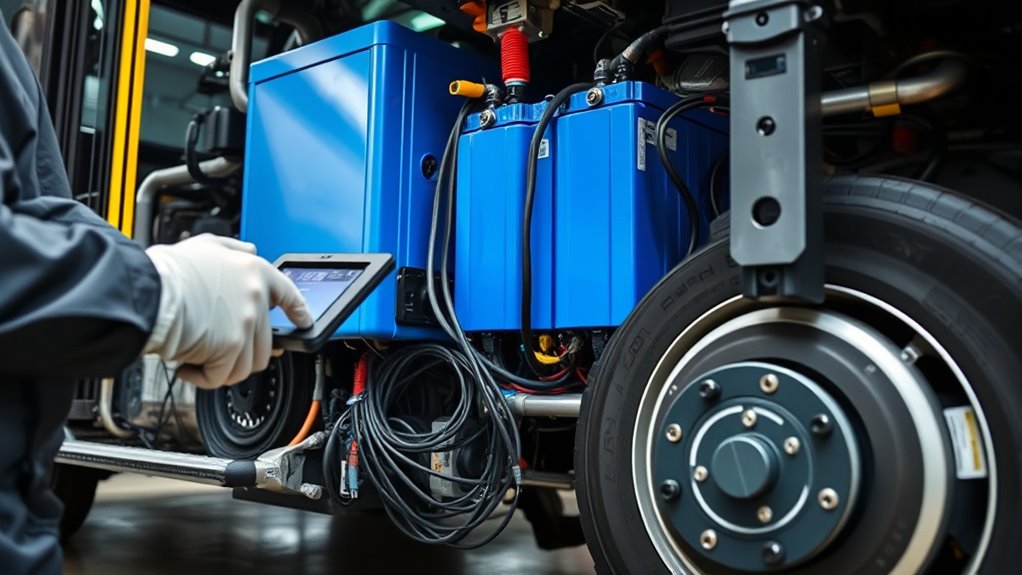
As electric buses become increasingly popular for their environmental benefits and energy efficiency, they also present unique maintenance challenges. Unlike traditional diesel buses, electric models have fewer moving parts, which can reduce some maintenance needs. However, this shift introduces specific issues that require attention.
Electric buses offer environmental benefits but bring unique maintenance challenges and technical demands.
For example, the drive motor, a crucial component, is often a source of trouble. Problems here can lead to costly replacements and operational delays. Additionally, alignment issues have been reported in some electric buses, impacting handling and efficiency. These problems may stem from manufacturing defects or wear over time and can be tricky to diagnose without specialized tools.
Supply chain disruptions and parts shortages further complicate maintenance. Many manufacturers have faced bankruptcies or recall issues, making it harder to source essential components. When parts are delayed or unavailable, buses stay out of service longer, affecting fleet reliability.
Charging system faults are another common concern. Malfunctioning chargers can cause significant downtime, especially if the infrastructure isn’t robust or compatible with different bus models. These issues highlight the importance of proactive maintenance and the need for reliable spare parts.
Maintaining battery health is a top priority for electric bus operators. Improper charging practices can accelerate battery degradation, reducing lifespan and increasing replacement costs. Regular electrical system checks are necessary to identify potential faults before they escalate into major failures.
Keeping software up to date also plays a crucial role in improving the efficiency and reliability of electric buses. Software updates often include bug fixes and performance enhancements that help prevent breakdowns. Moreover, advances in battery management systems have significantly improved overall durability and safety, but require skilled technicians to monitor and service effectively.
Technicians face a steep learning curve when working on electric buses. They need specialized training to understand the complex electrical systems and diagnostic tools. Access to advanced diagnostic equipment becomes essential for accurate troubleshooting, saving time and money.
Despite these technical requirements, many maintenance teams are still adapting to the new technology, which can lead to higher initial costs and longer repair times. Embracing ongoing technician training programs can help mitigate these challenges by ensuring staff stay current with evolving systems.
Operational reliability remains a concern, as high breakdown rates—some reports indicate 20% of electric school buses are out of service daily—raise questions about dependability. Manufacturer issues, recalls, and limited charging infrastructure add to these challenges. Furthermore, component quality varies between suppliers, impacting the longevity and performance of critical parts.
The need for extensive charging stations and upgraded electrical grids demands substantial investment, often constrained by tight budgets and logistical hurdles. Standardization problems in charging systems also complicate maintenance, requiring technicians to carry multiple adapters and tools.
Furthermore, the training of maintenance personnel is essential to keep pace with technological advancements and ensure timely repairs.
Frequently Asked Questions
How Often Should Electric Bus Batteries Be Serviced?
You should service your electric bus batteries regularly, based on usage and environmental factors. Typically, check battery health, voltage, and connections every 3 to 6 months, especially if you operate on high-mileage routes or in extreme temperatures.
Keep an eye on capacity loss and cooling system performance. Following the manufacturer’s guidelines and monitoring battery performance helps extend lifespan and prevents unexpected failures.
What Are Signs of Inverter Failure in Electric Buses?
Like a captain sensing rough seas, you notice signs of inverter failure in your electric bus. Watch for voltage imbalances, AC breaker trips, and overcurrent alarms during acceleration.
Keep an eye on the inverter’s annunciator and “EV Stop” indicator, which signal issues.
Physical clues include damaged cables, loose wiring, or burned components.
Diagnosing involves checking neutral lines, testing relays, and inspecting for burn marks or corrosion to keep your bus running smoothly.
How to Troubleshoot Charging Port Issues?
When troubleshooting charging port issues, start by inspecting the port for physical damage like bent pins or debris.
Confirm the port is clean and dry, and check for error codes.
Test different cables and charging stations to identify possible faults.
Make sure the connection is secure, and restart the vehicle and charger if needed.
If problems persist, consult a professional for further diagnosis and repair.
Are There Specific Maintenance Routines for Electric Bus Motors?
Did you know electric bus motors have fewer moving parts, reducing mechanical failures by up to 60%?
To keep them running smoothly, you should perform regular checks on electrical systems and coolant levels, and guarantee your technicians are trained with the latest diagnostic tools.
Inspect electrical components periodically and monitor for signs of wear.
Implementing these routines helps prevent issues before they cause costly downtime, ensuring peak performance and safety.
How to Prevent Software Glitches in Electric Bus Systems?
To prevent software glitches in electric bus systems, you should keep your software updated through automated OTA updates, guaranteeing you’re always running the latest patches.
Utilize predictive maintenance algorithms to spot issues early, and conduct regular cybersecurity audits to prevent malware.
Integrate AI-driven anomaly detection and cloud diagnostics for real-time monitoring, plus ensure firmware-hardware compatibility checks before updates.
These steps help maintain system stability and minimize glitches effectively.
Conclusion
To keep your electric buses running smoothly, you need to stay ahead of common maintenance issues like battery health and electrical system checks. Regular inspections, timely repairs, and proper training can make all the difference. Are you prepared to tackle these challenges before they become costly problems? By staying proactive, you guarantee reliable service, reduce downtime, and extend your fleet’s lifespan. After all, isn’t keeping your buses on the road better than dealing with unexpected breakdowns?