Common maintenance issues in electric buses include battery degradation, charging system faults, supply chain delays, software glitches, and high-voltage safety risks. To address these, implement regular battery monitoring, use reliable infrastructure, diversify suppliers, keep software updated, and follow strict safety protocols. You also need skilled technicians for complex repairs and preventive checks on mechanical components. Mastering these strategies will help you keep your fleet running smoothly—exploring these points further can boost your maintenance effectiveness.
Key Takeaways
- Regularly monitor battery health and implement proper charging practices to prevent capacity loss and extend lifespan.
- Conduct routine inspections of electrical systems, including connectors and wiring, to identify and address potential faults early.
- Ensure high-voltage safety protocols are followed during maintenance to prevent accidents and equipment damage.
- Schedule preventive maintenance such as cleaning terminals, checking voltage drops, and testing power components to avoid system failures.
- Maintain updated software and firmware to improve system reliability, performance, and fault detection capabilities.
Battery Degradation and Replacement Challenges
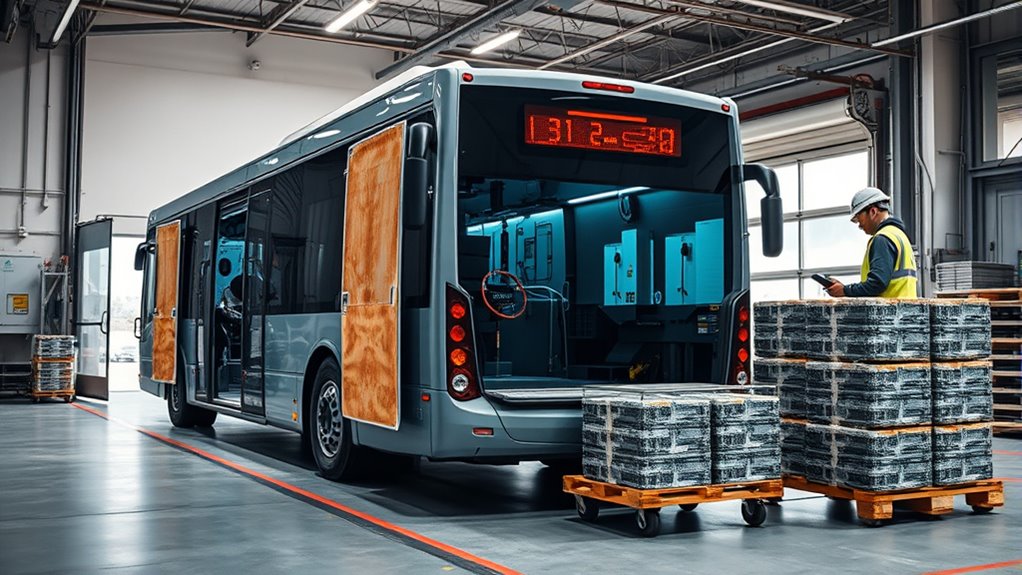
Battery degradation poses a significant challenge for electric bus operators because it directly reduces the vehicle’s operational range and increases maintenance costs.
As batteries age, their capacity declines, forcing you to schedule replacements sooner and spend more on repairs. Factors like deep discharges, rapid charging, high temperatures, and calendar aging accelerate this process. Proper charging practices are essential to minimize wear and tear on the battery cells.
Even when buses are idle, batteries degrade over time due to storage conditions. Managing battery health involves limiting full charge cycles, maintaining suitable temperature, and using slower charging methods to reduce stress. battery management systems can help monitor and optimize charging and discharging patterns, thereby prolonging battery life. These measures can extend battery lifespan, but eventual replacement remains inevitable. High replacement costs impact your operational budget, making it essential to monitor battery health regularly and plan for these expenses.
Proper management minimizes downtime and preserves your fleet’s efficiency. Additionally, ongoing research into AI Safety aims to develop smarter monitoring tools that can predict battery failures before they happen, further supporting maintenance efforts. Incorporating predictive analytics can aid in early detection of potential issues, saving costs and reducing unexpected outages.
Navigating Charging Infrastructure Reliability
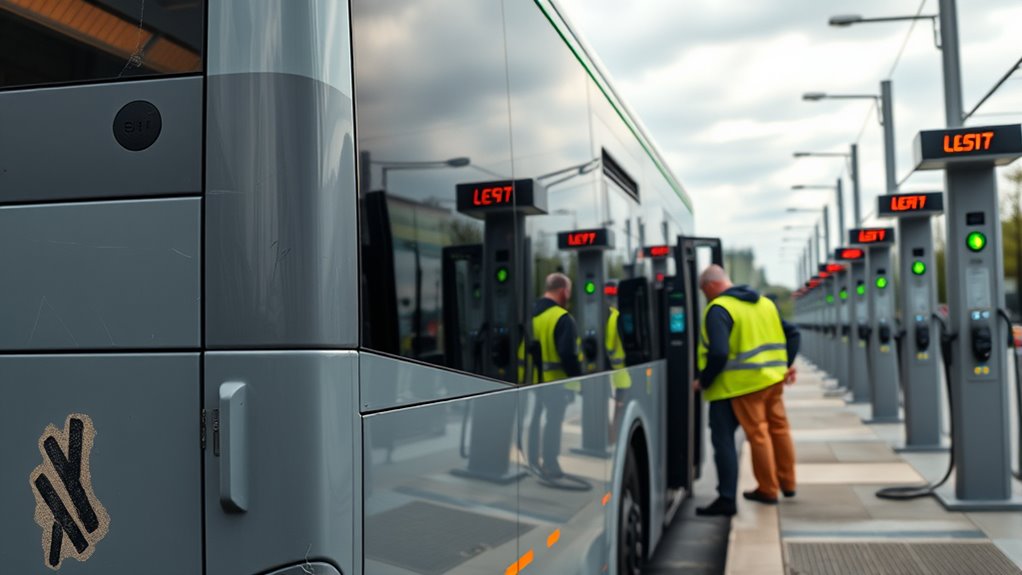
Ensuring reliable charging infrastructure is crucial for maintaining your fleet’s operational efficiency. High power demands can strain existing electrical grids, so utility upgrades are often necessary.
Modular charger designs, like Pii’s all-in-one cabinets, help reduce installation costs and simplify maintenance by streamlining components.
With a Mean Time Between Failures (MTBF) exceeding a million hours for key parts like rectifiers, uptime has improved.
Remote monitoring detects faulty components and connectivity issues early, enabling proactive repairs.
Operator behavior analytics help identify misalignment or bypasses, distinguishing user errors from hardware faults.
Managing downtime effectively involves categorizing issues by severity, enforcing SLAs, and using backup generators or redundant chargers.
These strategies ensure your charging infrastructure remains dependable, supporting consistent bus operation and reducing unexpected disruptions.
Overcoming Supply Chain and Part Shortages
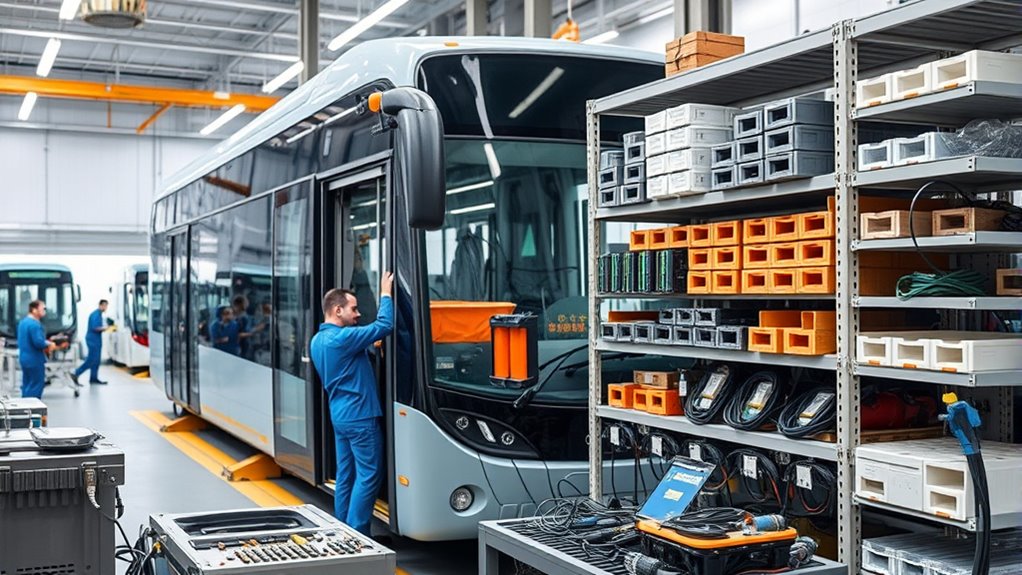
Maintaining reliable charging infrastructure depends heavily on a steady supply of quality components. Supply chain disruptions and increased demand for electric buses strain manufacturer inventories, leading to delays and shortages of critical parts. To address this, incorporating high-quality projectors into your planning can help visualize potential supply chain issues and improve logistical coordination. Recognizing the importance of vendor reliability in merchant services can also inform better decision-making and risk mitigation.
To overcome these challenges, diversify your suppliers to reduce dependency on a single source, and implement strong inventory management to keep essential parts on hand. Identify alternative components or substitutes to maintain production flow when specific parts are unavailable. Additionally, understanding the Gold IRA market can assist in financial planning and resource allocation during supply chain uncertainties. Awareness of IRA investing strategies can help optimize your financial resilience and ensure ongoing investment in your infrastructure.
Collaborate with other manufacturers for resource sharing and sourcing, and use predictive analytics to forecast potential shortages. Building transparency in your supply chain, establishing long-term contracts, and sourcing locally can improve stability.
Maintaining emergency stockpiles and forming strategic partnerships also enhance your ability to respond swiftly to supply disruptions.
Managing Software and Firmware Complexities
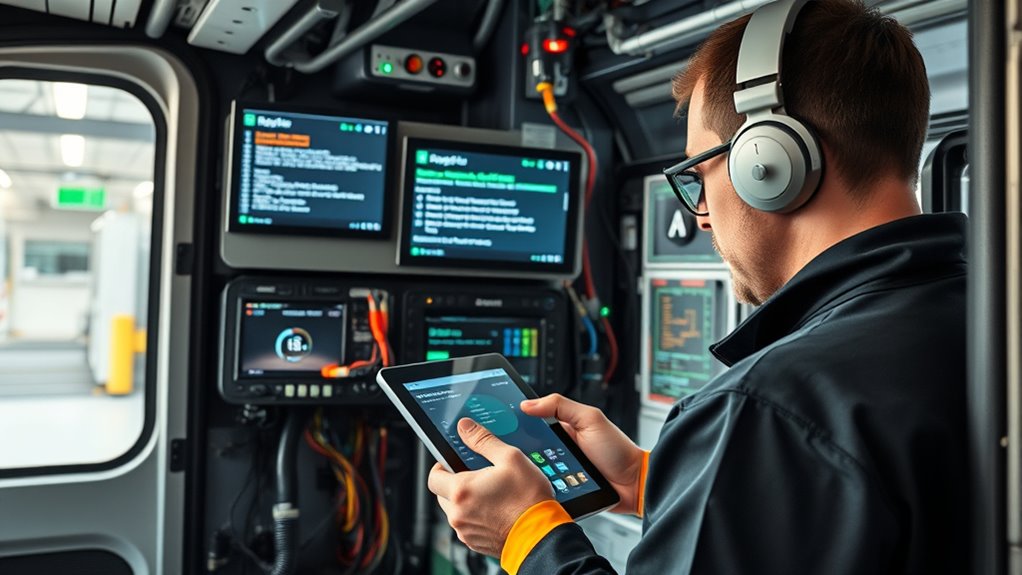
Managing software and firmware complexities is essential for keeping electric bus charging systems reliable and efficient. Automated firmware updates from platforms like Ampcontrol eliminate manual tasks and reduce disruptions, while bulk updates enable simultaneous upgrades across hundreds of stations, saving time. Automation technologies can also help streamline update processes and improve reliability. Rigorous testing in lab environments ensures updates are dependable and minimize risks. Compatibility is maintained through API-based platforms, allowing seamless integration with existing systems. To guarantee firmware reliability, adopting a proactive approach helps prevent failures and maintains consistent charging performance. Well-managed firmware enhances user experience, supports scalability, and prepares systems for future technologies. Additionally, extensive software solutions like Optibus facilitate real-time monitoring, analytics, and predictive maintenance, which optimize operations, reduce downtime, and lower energy costs. Proper management of these software and firmware complexities boosts overall charging infrastructure resilience. A thorough understanding of Gold IRA principles can also inform strategic planning for long-term infrastructure investments and security. Incorporating mindfulness techniques into maintenance workflows can also reduce stress and improve focus among technicians, enhancing overall system management.
Addressing Specialized Labor and Certification Needs
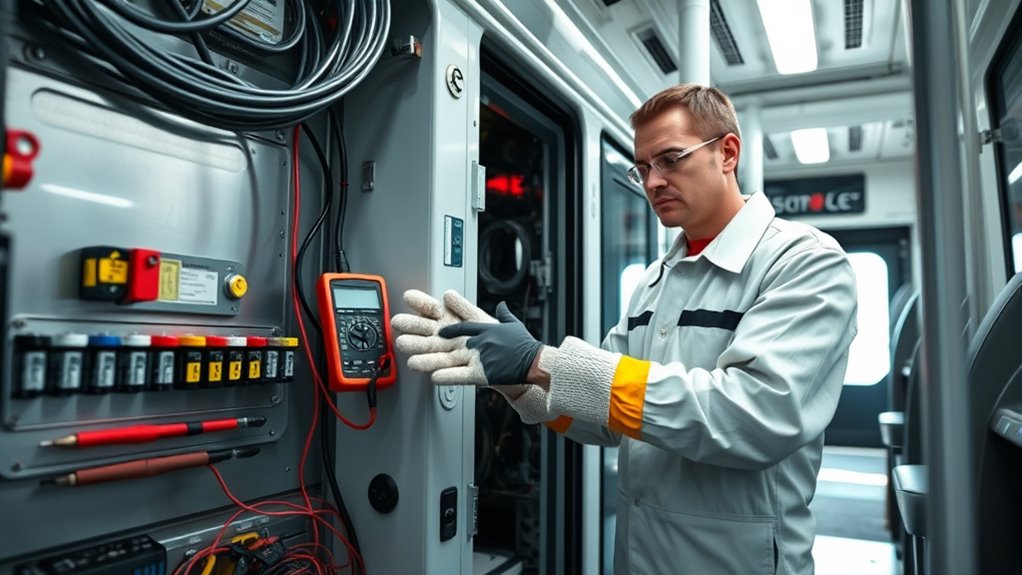
As electric bus fleets expand, addressing the specialized labor and certification needs becomes increasingly critical. Shifting from diesel to electric requires your technicians to acquire new skills, but there’s a shortage of qualified workers in this field. Collaborating with manufacturers, educational institutions, and industry groups is essential to develop effective training programs. You also need certified technicians to guarantee quality maintenance, which calls for establishing clear certification standards and ongoing training to keep up with rapid technological advances. To ensure the highest standards, integrating vetted training programs for electric vehicle maintenance can help build a qualified workforce that meets industry demands. Developing a comprehensive understanding of electric vehicle technology is crucial for technicians to perform effective diagnostics and repairs. Incorporating specialized diagnostic tools into your training can further enhance technician capabilities and maintenance precision. Implementing AI security in training platforms can help protect sensitive educational data and ensure secure access to resources. Competition from private fleets and lower wages in school districts make retaining skilled staff challenging. To overcome this, you should focus on improving job quality, creating career pathways, and forming industry partnerships that attract and retain qualified technicians in the public sector.
Balancing Mechanical Wear and New System Vulnerabilities
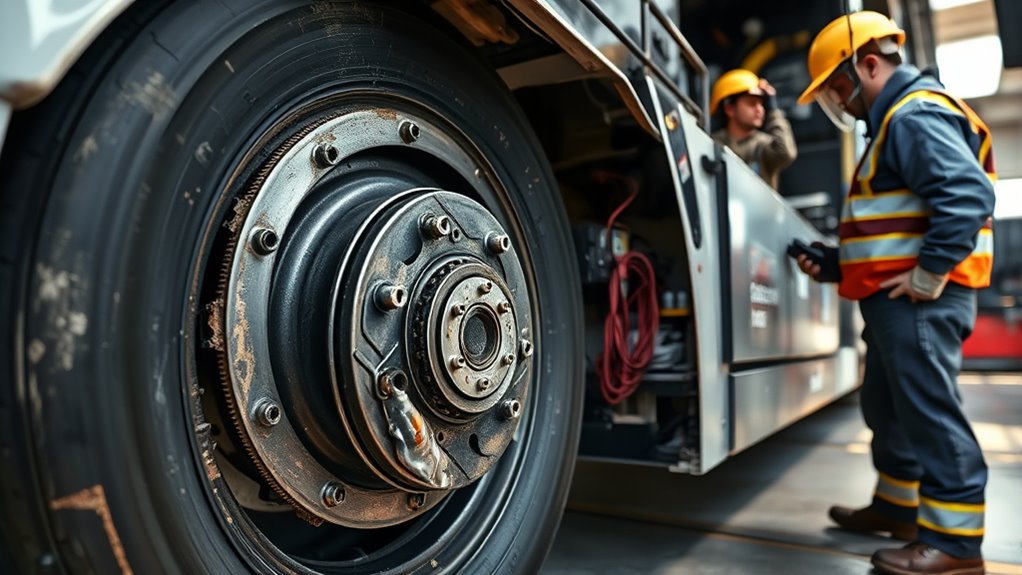
Expanding electric bus fleets brings new maintenance challenges alongside traditional mechanical concerns. You’ll need to manage mechanical wear, which can accelerate due to increased usage and exposure to harsh weather, impacting components like brakes and drivetrains. Inadequate pre-purchase testing may lead to unforeseen issues, such as wiring harness failures or battery performance drops in cold or hot conditions. Frequent software updates are necessary to address vulnerabilities and improve reliability, but they can also introduce new bugs. Batteries tend to degrade faster under extreme temperatures, reducing range and efficiency. Additionally, battery technology is rapidly evolving, requiring maintenance teams to stay updated on the latest advancements to ensure optimal performance. Proper diagnostics can help detect early signs of system degradation before failures occur, saving costs and downtime. Implementing dynamic communication exercises can also foster better teamwork among maintenance staff, improving overall response times and problem-solving capabilities. Regular training on modern heat pump systems can further enhance system understanding and troubleshooting skills, which is equally applicable to electric bus maintenance teams adapting to new technologies.
Handling Proprietary Systems and Repair Limitations
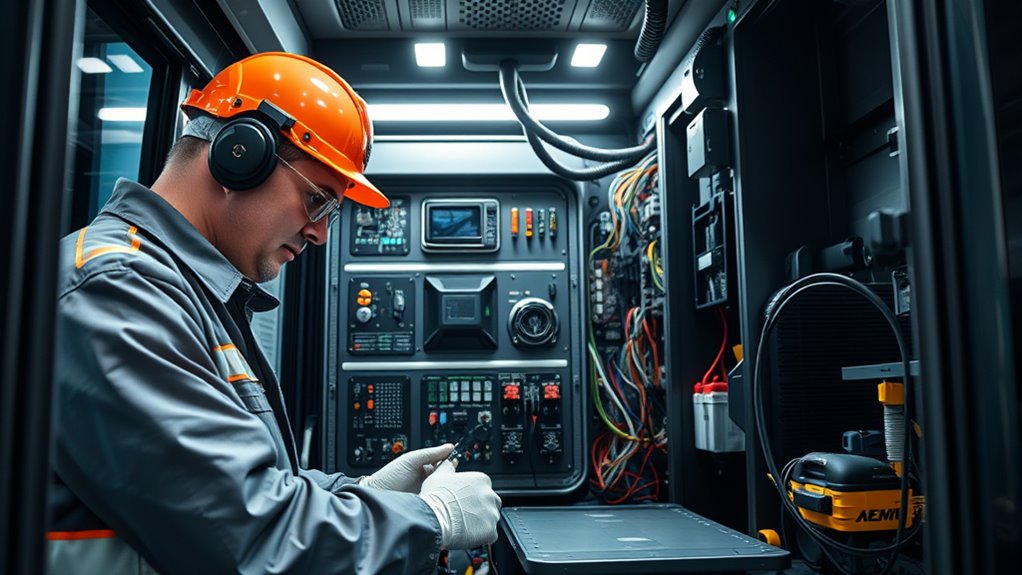
Handling proprietary systems in electric buses often poses significant maintenance challenges because specialized technology limits access to repairs and parts. These systems can restrict your ability to find compatible replacement components, leading to delays and increased costs. Additionally, retail hours information can be useful for scheduling maintenance appointments and sourcing parts from suppliers during optimal times. The software and diagnostic tools required are often exclusive to the manufacturer, making troubleshooting more complex and requiring specific training for your technicians. Dependence on manufacturer support can cause delays if resources aren’t readily available. To overcome these issues, consider developing open standards and fostering strong relationships with manufacturers for quicker support. Investing in local expertise and third-party support networks can also improve maintenance flexibility. Standardizing platforms across your fleet simplifies repairs and reduces dependency on proprietary systems, helping you maintain your buses more efficiently. Incorporating safety protocols and ensuring technicians are trained in the latest diagnostic procedures can further mitigate downtime and improve overall maintenance outcomes. Moreover, implementing training programs for your maintenance staff can enhance their ability to work with complex proprietary systems and reduce downtime.
Ensuring Safety in High-Voltage Maintenance
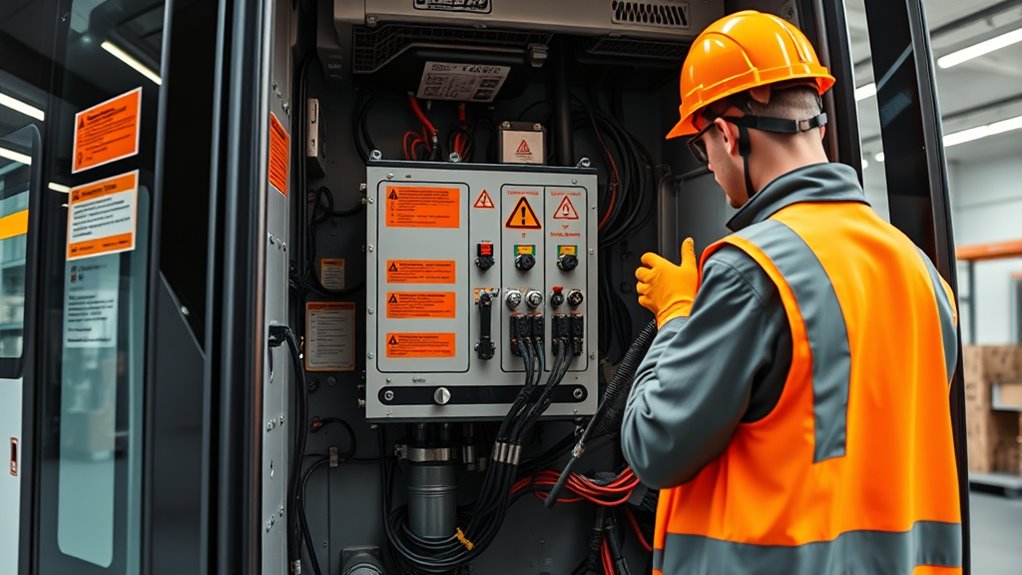
Ensuring safety during high-voltage maintenance is essential to prevent accidents and injuries. You must always verify the presence of warning symbols on high-voltage components, which indicate potential risks.
Always verify warning symbols on high-voltage components to ensure safety and prevent accidents.
Before working, disconnect power sources and confirm a voltage-free condition using proper testing tools. High-voltage systems operate at up to 400 volts DC, so strict adherence to safety protocols is critical.
Use PPE such as insulated gloves and tools rated for high-voltage work, and ensure warning signs are visible around maintenance areas. Follow lockout/tagout procedures to prevent accidental energization.
Only trained, certified personnel should handle high-voltage tasks, and regularly update training to stay compliant with standards like NFPA 70E.
Implementing these measures minimizes risks and keeps your team safe during maintenance.
Implementing Effective Preventive Maintenance Strategies
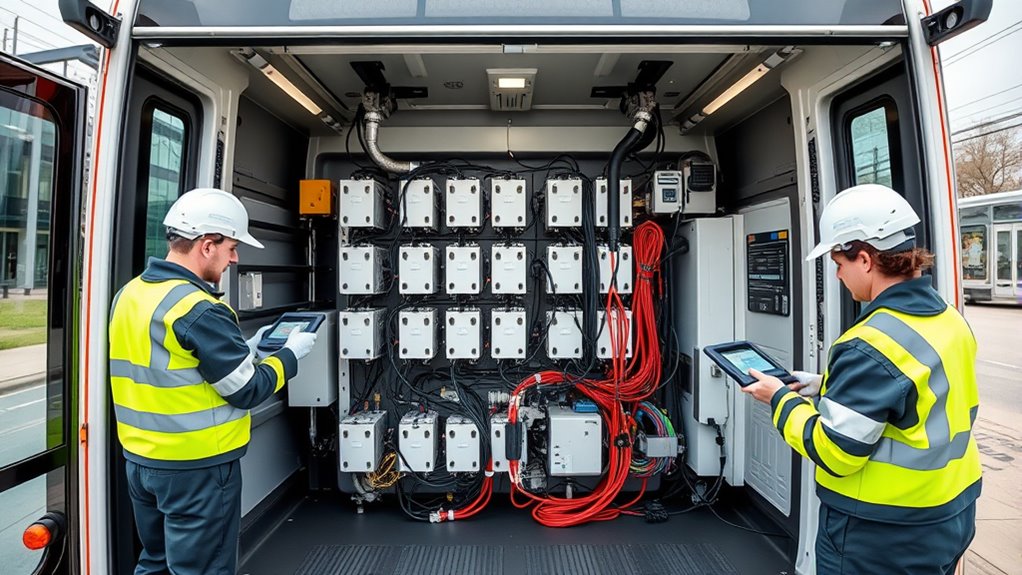
Implementing effective preventive maintenance strategies is essential to keep electric buses operating reliably and safely. Start by performing regular electrical insulation checks to prevent leaks and short circuits.
Monitor power distribution units (PDUs) and verify converter outputs for 12V and 24V systems to ensure proper function. Keep battery terminals clean and inspect them regularly to prevent voltage drops.
Check CAN communication signals to maintain seamless subsystem interactions. Use real-time data collection sensors and advanced analytics to predict potential issues early.
Focus on battery health by monitoring degradation and promoting ideal driving behaviors to extend battery life. Maintain a dependable charging infrastructure and adapt maintenance routines for seasonal changes.
These proactive steps help reduce breakdowns, maximize performance, and enhance your fleet’s operational efficiency.
Frequently Asked Questions
How Can Fleets Reduce Battery Degradation Over Time?
To reduce battery degradation over time, you should follow best practices like maintaining state of charge between 10-90%, avoiding frequent fast-charging, and not storing batteries at 100% SOC.
Additionally, plan routes to prevent thermal stress, use active cooling, and monitor cell temperatures in real-time.
Minimize aggressive driving behaviors, optimize regenerative braking, and schedule regular health checks to catch issues early, extending your battery’s lifespan.
What Are Best Practices for Maintaining Charging Stations?
You should regularly monitor and inspect your charging stations to guarantee peak performance. Keep ports clean and free of debris, especially in harsh environments.
Update firmware and software promptly, and manage cables securely to prevent damage.
Schedule preventive maintenance during off-peak hours, track usage through remote systems, and stock critical spare parts.
Proper weatherproofing and staff training are essential to avoid costly repairs and maximize uptime.
How Do Supply Chain Issues Affect Bus Downtime and Repairs?
Supply chain issues directly increase your bus downtime and complicate repairs. When vital parts like batteries or proprietary components are unavailable or delayed, your fleet can’t operate efficiently.
You might face extended waits, resorting to cannibalizing buses or relying on third-party alternatives that may not fit perfectly. These disruptions strain your maintenance schedules, increase costs, and reduce service reliability.
Making it essential to develop alternative sourcing strategies and stockpile essential parts whenever possible.
What Training Is Needed for Technicians to Service Electric Buses?
Imagine standing next to an electric bus, cables buzzing, ready for maintenance. You need training in high voltage safety, battery systems, and propulsion to work confidently.
Level 1 and 2 courses cover these essentials, including lockout/tagout procedures and PPE.
Continuous learning keeps you updated on evolving technology.
Hands-on and OEM-specific training deepen your skills, ensuring safety and efficiency in servicing these advanced vehicles.
How Can Safety Risks Be Minimized During High-Voltage Maintenance?
You can minimize safety risks during high-voltage maintenance by following strict safety protocols. Always guarantee the system is de-energized and use proper testing equipment before starting work.
Wear appropriate safety gear, display warning signs, and handle high-voltage cabling carefully.
Regularly inspect equipment, stay updated with training, and adhere to safety policies.
Planning emergency procedures and maintaining clear documentation also help prevent accidents and protect everyone involved.
Conclusion
To keep your electric buses running smoothly, stay proactive with regular maintenance and stay ahead of common issues like battery wear and charging hiccups. Think of it as tending a garden—you’ll need to nurture and address problems early to prevent weeds from taking over. By understanding these challenges and implementing smart strategies, you’ll ensure your fleet stays reliable and efficient, turning maintenance into a well-oiled machine rather than a thicket of headaches.