When troubleshooting electrical faults in electric buses, start by inspecting the battery and charging system, checking for damaged cables and proper connections. Next, verify CAN bus communication—you’ll want to measure resistance and confirm all devices share a common ground. Examine wiring integrity with visual checks and thermal scans, and evaluate the electronic control modules for software issues or fault codes. Following these steps will help you identify the root cause and fix the problem efficiently.
Key Takeaways
- Conduct visual inspections of wiring, connectors, and high-voltage components for damage, corrosion, or loose connections.
- Use a multimeter or CAN bus analyzer to check for proper resistance, signal integrity, and communication errors.
- Verify grounding, termination resistors, and bus wiring to ensure correct setup and prevent communication failures.
- Review sensor data and fault codes via diagnostic tools like OBD-II to identify specific electrical issues.
- Follow safety protocols, including PPE and lockout/tagout procedures, during troubleshooting to prevent electrical hazards.
Assessing the Battery and Charging System
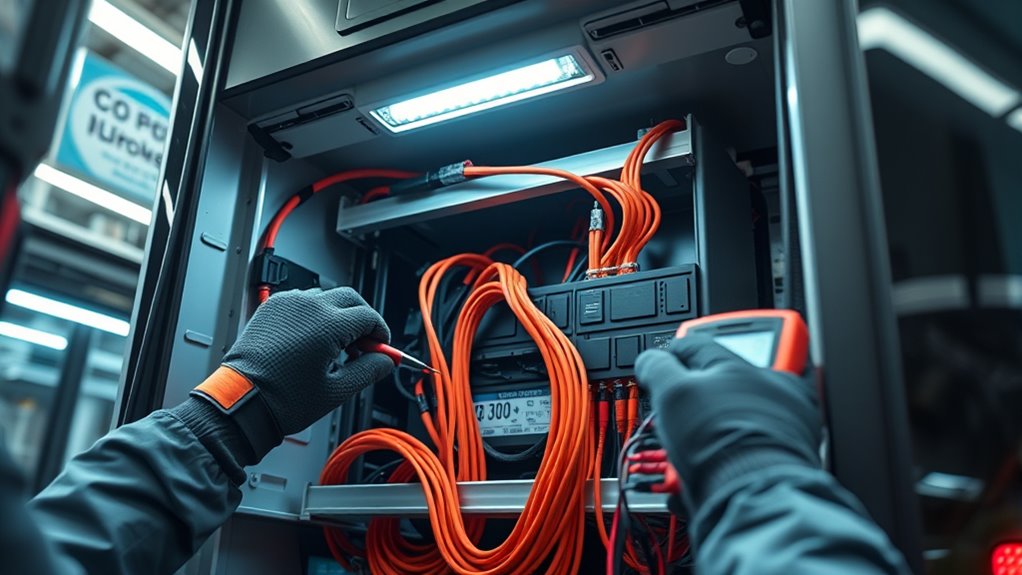
Evaluating the battery and charging system is essential for ensuring the reliability and safety of electric buses. You should regularly perform maintenance checks using the entropy weight method to identify key performance indicators across reliability, economy, and security. Incorporating GMC tuning techniques can help optimize the electrical systems for better performance and longevity. Additionally, understanding the types of charging infrastructure available can aid in selecting the most compatible and efficient options for your fleet. For example, selecting the appropriate charging connector types ensures seamless integration with existing infrastructure and minimizes compatibility issues. Recognizing potential cost implications linked to different charging solutions can help in budget planning and cost management.
Regular maintenance checks are vital for ensuring electric bus battery safety and reliability.
Collecting daily operation data over 50+ days helps you track real-world performance and detect early issues.
Monitoring battery condition involves analyzing cycle life and thermal management to prevent premature aging and overheating.
Appraising charging infrastructure compatibility ensures your buses match voltage and current specifications, reducing risks during charging.
Additionally, conducting Fire Hazard Analysis (FHA) per NFPA 551 standards helps you identify and mitigate fire risks.
These steps ensure your battery and charging systems operate efficiently, safely, and reliably over the bus’s lifespan.
Diagnosing CAN BUS Communication Failures
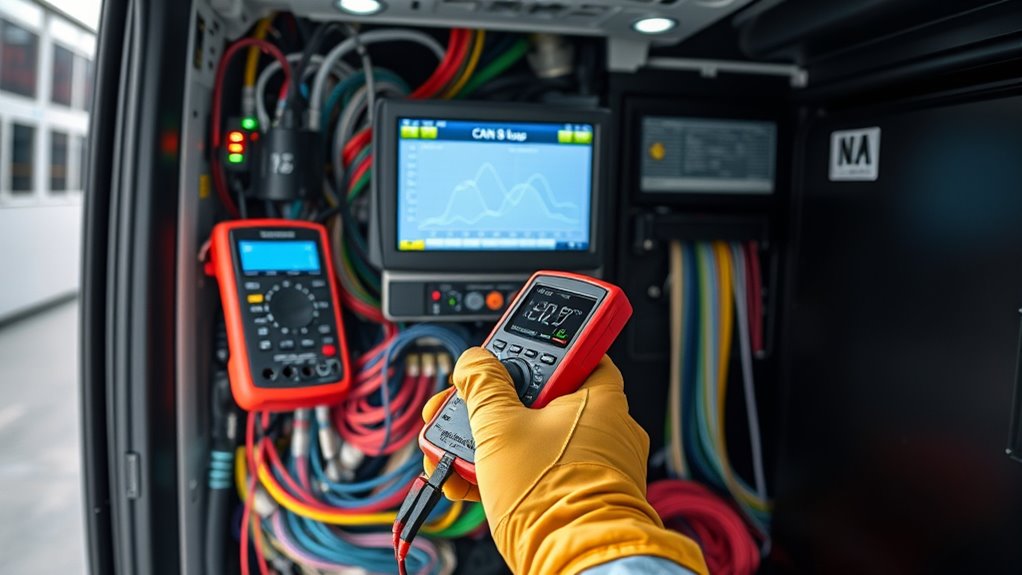
How can you effectively diagnose CAN BUS communication failures in electric buses? Start by measuring resistance between CANH and CANL with the power off; a reading around 60 ohms indicates proper termination.
Check that all devices share a common ground potential to prevent noise and communication errors. Use a multimeter to verify voltage levels and a CAN bus analyzer or oscilloscope to examine signal waveforms for irregularities or reflections.
Ensure all connected devices operate at the same data rate, as mismatched speeds cause issues. Confirm the correct termination resistors are installed at both ends of the bus, typically 120 ohms, to prevent signal reflections.
Inspecting Wiring and Connection Integrity
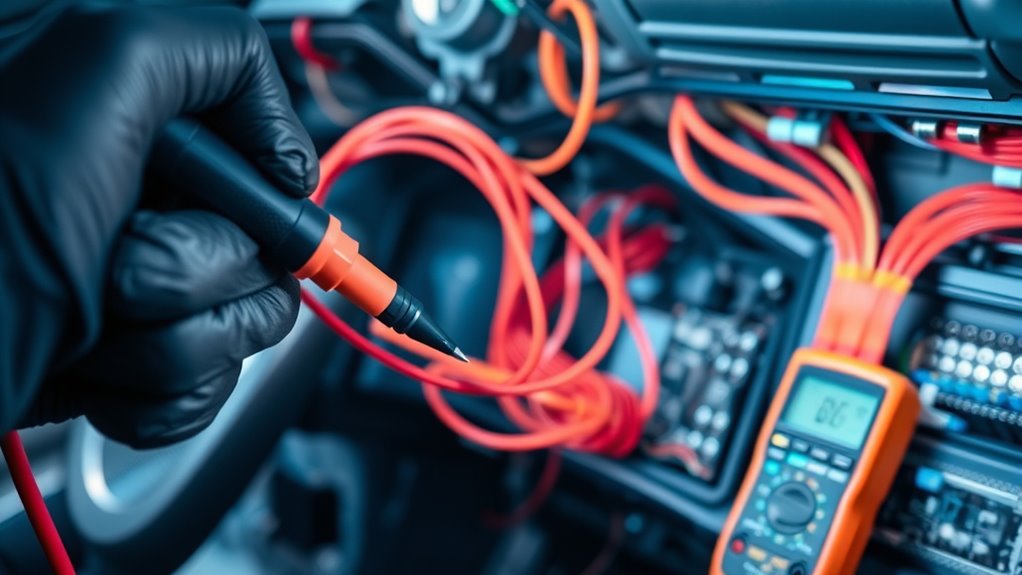
Inspecting wiring and connection integrity is a critical step in ensuring the reliable operation of your electric bus’s high-voltage system. Start by examining orange-colored cables, which indicate high-voltage components, for any signs of damage. Use stretching or rolling gloves to check for cracks or tears during HV work, especially around key areas like charging receptacles, contactors, and fuse connections. Additionally, verifying the support hours of your maintenance team can help ensure prompt assistance if issues arise. Focus on components such as BMC, CCU, and SCM near charging ports, as these are priority zones. Document any wear patterns on terminals to track potential issues over time. Conduct visual inspections complemented by thermal imaging scans of floor-level bus ducts and high-voltage panels—preferably on overcast mornings or early evenings. Confirm all connections are secure and free of corrosion before proceeding with further diagnostics. Regular inspection routines are essential to maintain system safety and performance. Incorporating regional expertise in your maintenance team can also improve fault detection accuracy. Additionally, performing preventive maintenance can help identify potential issues before they lead to failures.
Evaluating Electronic Control Modules and Software
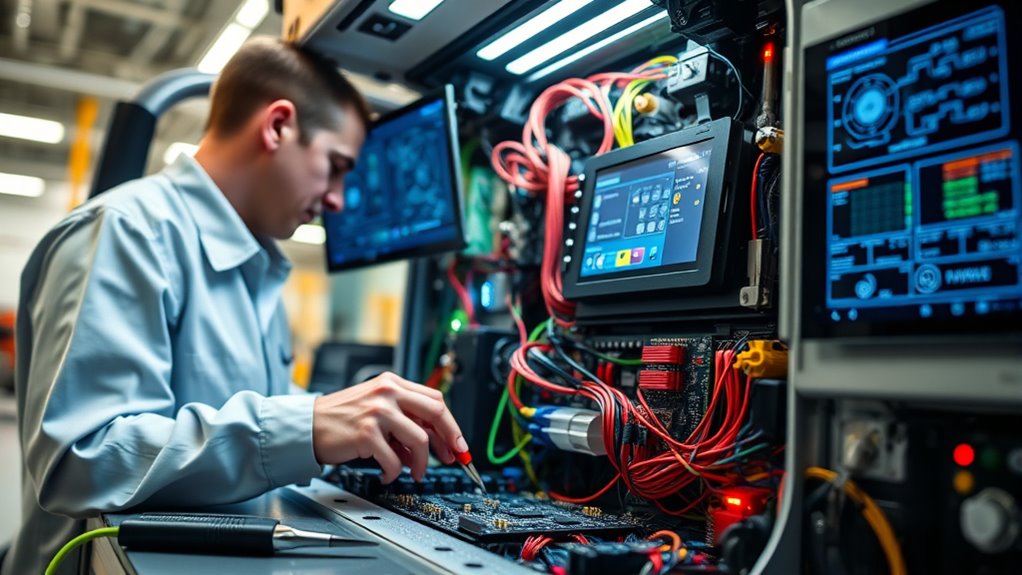
Evaluating the performance of electronic control modules (ECMs) and their software is essential for maintaining the reliable operation of your electric bus’s high-voltage system. You should regularly check the ECM’s microcontroller processing by reviewing sensor data handling, ensuring real-time management of torque and speed. Use diagnostic tools like OBD-II to retrieve fault codes quickly and verify the accuracy of fault logging functions. Inspect software updates through firmware validation and checksum comparisons to prevent corruption. Pay attention to adaptive learning features that optimize performance based on sensor feedback. Utilize data visualization dashboards to monitor real-time metrics such as voltage and temperature. Leverage predictive analytics to catch potential failures early. Proper evaluation helps you identify software issues before they lead to system faults or downtime. Incorporating HEPA filtration principles can help in diagnosing and controlling particulate-related faults in the system, ensuring cleaner operation and component longevity. Additionally, assessing the integrity of software security measures is crucial to prevent malicious interference or unauthorized access that could compromise system stability.
Implementing Preventive Maintenance and Safety Protocols
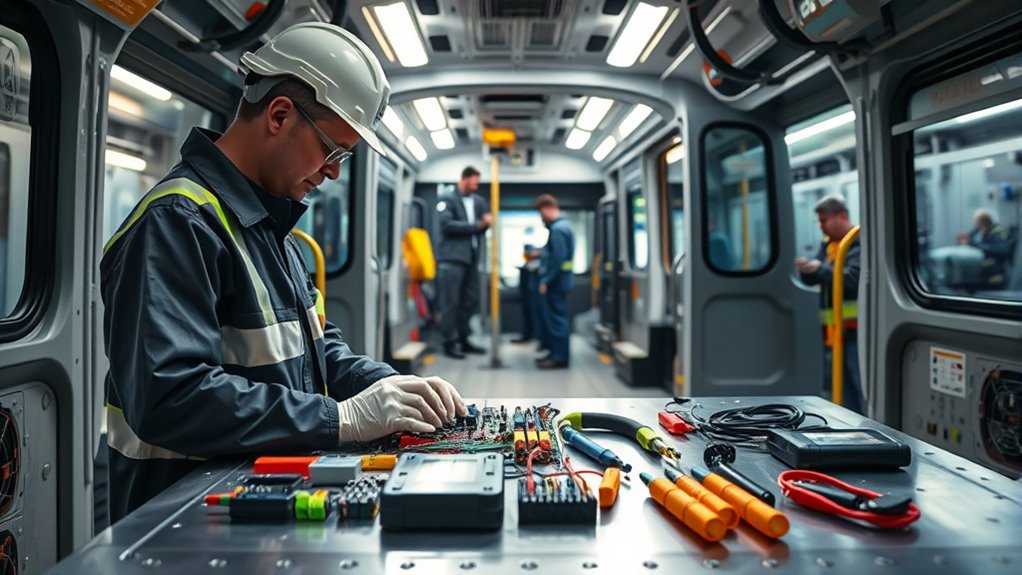
Implementing effective preventive maintenance and safety protocols is essential for ensuring the reliable and safe operation of electric buses. You should schedule regular inspections to catch issues early, such as checking electrical connections, insulations, and battery health.
Regular inspections are vital for safe, reliable electric bus operation.
Lubricate mechanical parts like gearboxes to keep them running smoothly, and maintain coolant systems for liquid-cooled drives. During maintenance, always wear PPE, follow lockout/tagout procedures, and use electrical safety tools like multimeters.
Train technicians thoroughly on electric bus systems to minimize risks. Develop emergency response plans for shocks or fires. Conducting industry-specific training helps ensure personnel are prepared for electrical emergencies.
Additionally, adopt predictive strategies by collecting real-time data and scheduling condition-based maintenance. These measures help prevent failures, reduce costs, and guarantee safety, keeping your fleet operating efficiently and securely. Staying updated on grocery store hours and other relevant industry information can also improve operational planning and safety compliance.
Understanding preventive maintenance can also motivate teams to adhere to safety protocols and continuously improve maintenance practices.
Frequently Asked Questions
How Can I Identify a Faulty Ground Connection Quickly?
When you want to identify a faulty ground connection quickly, start with a visual inspection for corrosion, loose or damaged wiring.
Use a multimeter to check for voltage drops or high resistance at ground points.
You can also perform ground loop detection to spot differences between grounds.
Regularly testing connections with specialized tools like ground loop detectors or thermal imaging helps you pinpoint issues efficiently.
What Are Signs of Alternator Failure in an Electric Bus?
Ever wondered what it feels like when your bus’s electrical system starts failing? Signs include warning lights on the dashboard, dim or flickering lights, and electrical malfunctions like radio or A/C issues.
You might also notice strange noises from the alternator or a dead battery that keeps losing charge. If you see these symptoms, it’s a clear sign that your alternator isn’t working properly and needs immediate attention.
How Do I Interpret OBD2 Error Codes Related to Electrical Faults?
When you interpret OBD2 error codes related to electrical faults, look for codes starting with U, which often indicate network or communication issues. For example, U1100 points to ECU communication problems.
Use an OBD2 scanner to retrieve these codes, then consult wiring diagrams and check connections, wiring, and batteries.
If needed, measure voltages with a multimeter to pinpoint electrical issues, and follow manufacturer guidelines for repairs.
What Tools Are Best for Diagnosing Complex Wiring Issues?
You’re facing a wiring maze that seems impossible to conquer, but the right tools make all the difference. Digital multimeters and oscilloscopes are your best allies for testing and analyzing signals.
Wiring diagrams and component info guide your path, while specialized equipment like OBD2 breakout boxes and semi-rugged laptops keep you connected and efficient.
With these tools, complex wiring issues become manageable, turning chaos into clarity.
How Often Should Electronic Control Modules Be Updated or Serviced?
You should update or service electronic control modules based on manufacturer recommendations, usage patterns, and environmental conditions. Regular checks are essential, especially for high-usage buses or those operating in harsh environments.
Keep detailed records of update schedules and use diagnostic tools to identify issues early. Frequent servicing ensures reliability, safety, and efficiency, helping you maintain ideal performance and comply with safety standards.
Stay proactive with your ECU maintenance to prevent costly faults.
Conclusion
Think of troubleshooting your electric bus like tending a garden; each component is a crucial plant needing attention. When you spot a fault early—like a wilted leaf—you prevent larger issues, much like catching electrical faults before they cause a breakdown. Regular checks and preventive care keep your system thriving, ensuring safe, reliable rides. Remember, just as a healthy garden blooms, a well-maintained bus runs smoothly and safely for miles to come.