In electric bus manufacturing, embracing the circular economy means designing for easy maintenance, recycling, and reuse of materials like batteries and plastics. You focus on extending battery life through smart operations and innovative recycling processes that recover critical metals. Industry collaborations and strict standards support responsible sourcing and waste reduction. This approach not only cuts environmental impact but also offers economic benefits. Keep exploring to uncover how these practices transform sustainable mobility.
Key Takeaways
- Designing buses with recyclable materials and easy maintenance to facilitate reuse, recycling, and waste reduction.
- Implementing closed-loop systems that recycle and repurpose battery materials back into new batteries.
- Developing second-life battery applications for energy storage and grid support, extending battery lifespan.
- Adhering to standards like ISO22628 and EU regulations to ensure recyclability and transparency in manufacturing.
- Promoting stakeholder collaboration across the supply chain to foster shared responsibility and sustainable practices.
Principles and Hierarchies Guiding Circular Practices in Bus Production
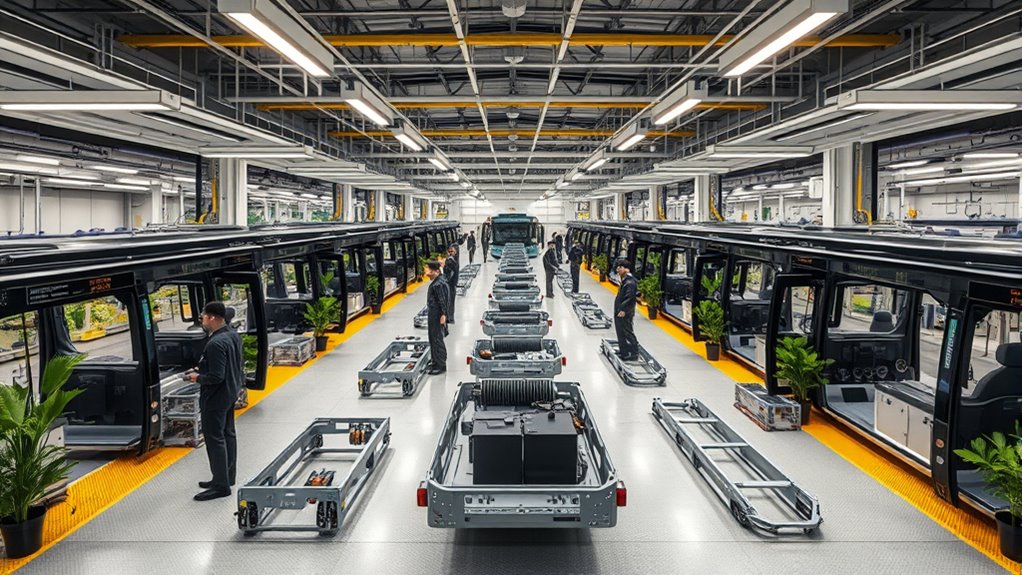
Understanding the principles and hierarchies guiding circular practices in bus production is essential for advancing sustainability in the industry. You focus on designing for circularity by creating buses that make maintenance and recycling straightforward.
Designing buses for easy maintenance and recycling advances industry sustainability.
Selecting recyclable or reusable materials plays a crucial role in reducing waste, while energy-efficient manufacturing minimizes environmental impact. Incorporating recyclable materials into design processes facilitates easier end-of-life processing and supports material recovery efforts. Additionally, the choice of materials influences the overall color accuracy of the final product, ensuring that visual and functional qualities meet standards.
Implementing closed-loop systems allows materials to be continually cycled back into production, conserving resources. These systems help reduce dependency on virgin resources and minimize waste generation. Employing material recovery strategies further enhances the efficiency of resource use and supports the circular economy.
Stakeholder engagement ensures that suppliers, manufacturers, and users work together to promote sustainability. Collaboration across the supply chain enhances the effectiveness of circular initiatives and promotes shared responsibility.
The hierarchy emphasizes prevention through efficient processes, sharing to reduce resource use, reuse of parts, remanufacturing to extend component life, and recycling at the end of life. Prioritizing prevention and reuse aligns with the goal of minimizing environmental impact throughout the product lifecycle.
Adopting these principles and hierarchies helps you build more sustainable, efficient electric buses aligned with circular economy goals. Additionally, understanding how juice extraction maximizes nutrient intake can inform the development of sustainable resource practices within manufacturing processes.
Extending Battery Lifespan Through Maintenance and Reuse Strategies
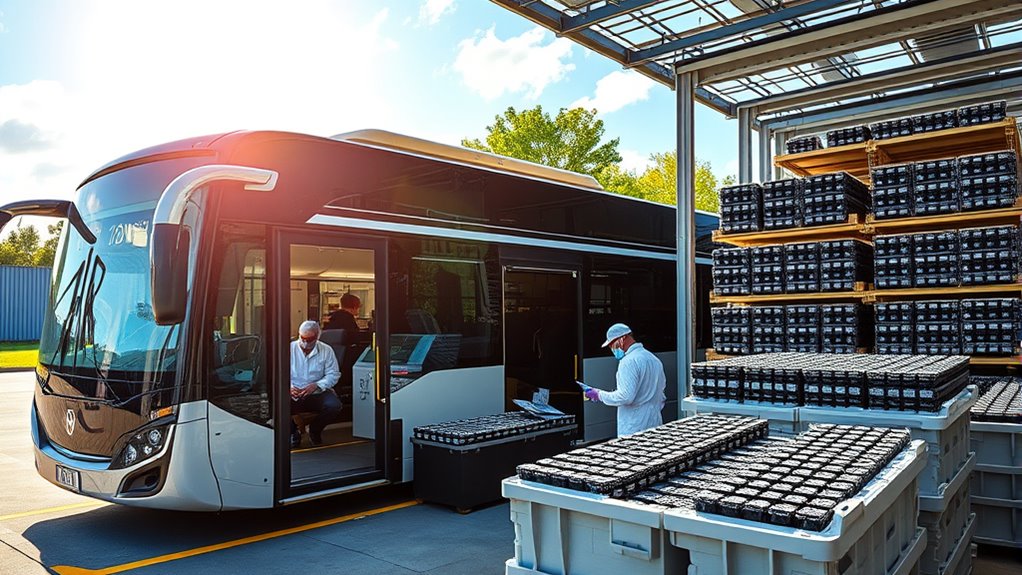
Extending the lifespan of electric bus batteries is essential for advancing circular economy practices in bus manufacturing, and effective maintenance and reuse strategies play a critical role in this effort. You can maximize battery life by running vehicles on varied routes, ensuring even degradation and delaying replacements. Operating batteries within 10-90% state of charge (SOC) minimizes wear, while avoiding high-speed charging reduces degradation. Preconditioning batteries before use enhances performance and longevity. Real-time data analysis enables predictive maintenance, helping you address issues early. Monitoring battery performance and adjusting driving behavior, like avoiding aggressive driving, can cut degradation by up to 25%. Maintaining ideal temperature and SOC levels during storage and charging further extends battery life, supporting reuse and reducing waste in line with circular economy goals. Incorporating advanced sound design techniques such as real-time data analysis and environmental monitoring can further optimize battery management systems for longevity.
Innovative Recycling Technologies and Material Recovery Processes
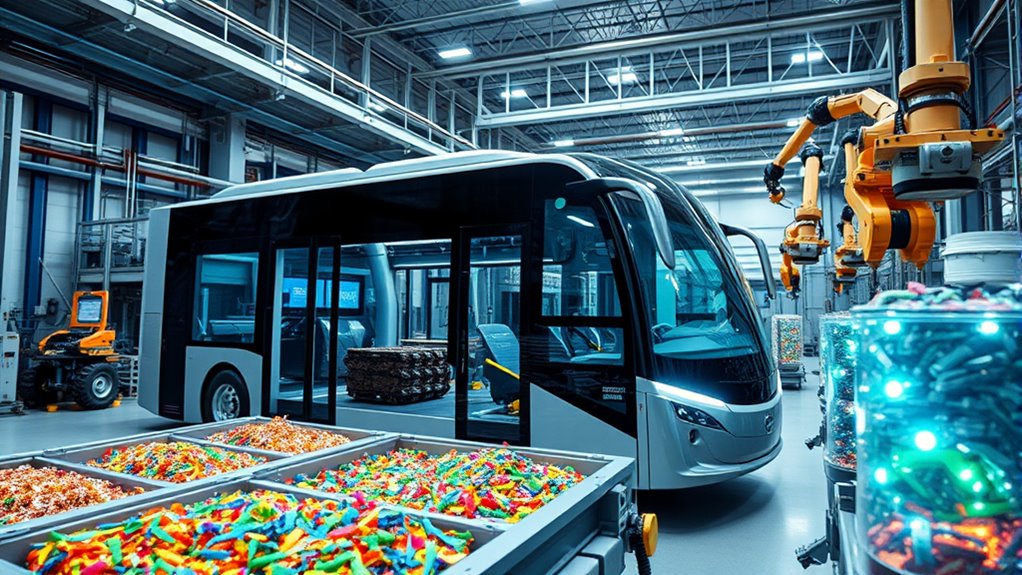
Innovative recycling technologies are transforming how you recover and reuse materials from electric bus batteries, reinforcing circular economy principles. Lithion’s process achieves a 98% critical mineral recovery rate, making it highly efficient. Their closed-loop system repurposes recovered materials directly into new batteries, reducing reliance on virgin resources.
At their Saint-Bruno facility, they handle collection, transport, and recycling for Nova Bus fleets across Canada, exemplifying large-scale impact. Automated disassembly and chemical hydrometallurgy enable you to extract metals like cobalt, nickel, lithium, and manganese, while recycling plastic casings minimizes waste.
Industry partnerships, such as those with Nova Bus and Girardin Bus, help scale these innovations and meet OEM standards. These advancements considerably cut environmental impacts, lower costs, and support sustainable, circular approaches to electric bus manufacturing.
Regulatory Frameworks and Industry Standards Supporting Circularity
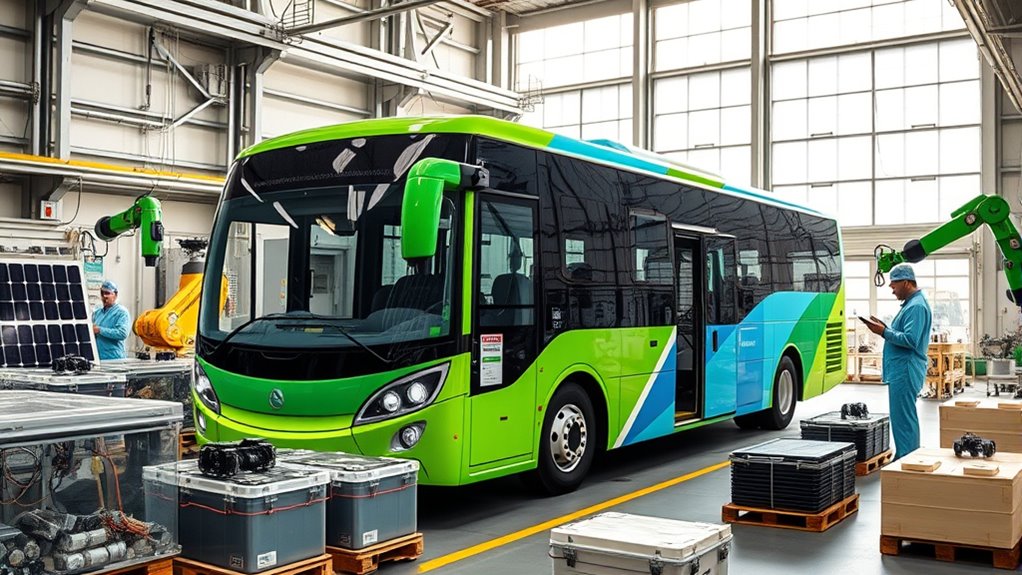
Regulatory frameworks and industry standards play a crucial role in fostering circularity within electric bus manufacturing by setting clear requirements for battery durability, safety, and recyclability. They ensure batteries meet minimum durability criteria, preventing low-quality, short-lived options that hinder resource efficiency.
Standards like ECE R100 and EU regulations enforce safety, performance, and recyclability metrics, guiding manufacturers toward sustainable practices. Incorporating these standards into national legislation strengthens compliance and promotes high-quality production.
Additionally, industry-specific standards for life cycle assessment, such as ISO22628, help evaluate environmental impacts and recyclability indexes. These frameworks incentivize reuse, recycling, and circular supply chains, supporting extended product lifespans and resource recovery.
Moreover, Personality Traits such as active listening and empathy are increasingly recognized as essential components for fostering collaboration and innovation in sustainable manufacturing practices. These interpersonal skills can enhance stakeholder engagement and facilitate the adoption of circular economy principles across the industry. Incorporating regulatory compliance as a foundational element further encourages manufacturers to align their processes with sustainability goals, ensuring industry-wide adoption of circular practices. Ultimately, they align industry practices with circular economy principles, driving sustainable innovation in electric bus manufacturing.
Overcoming Sustainability Challenges in Raw Material Extraction and Processing
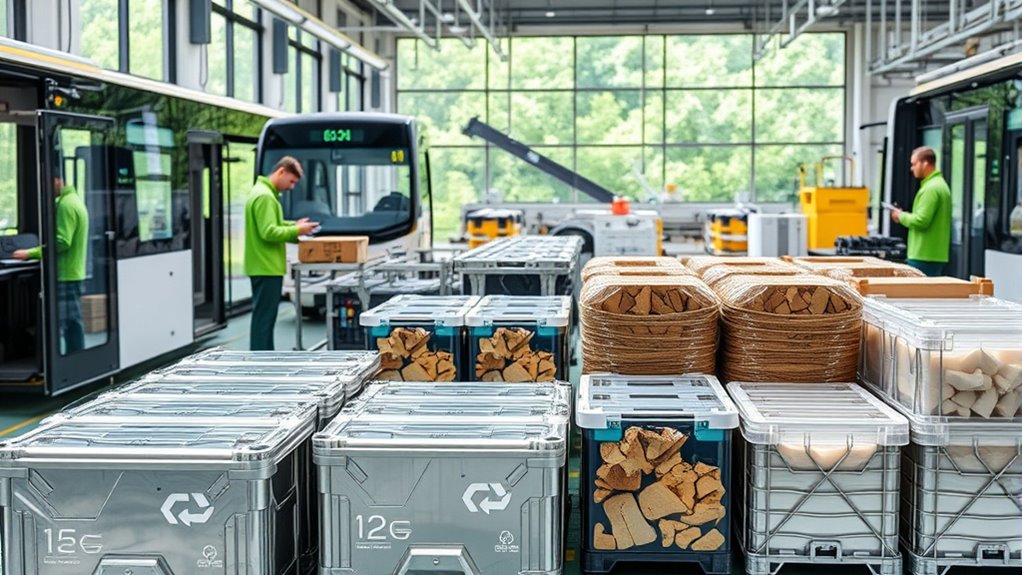
While regulatory frameworks guarantee that batteries meet safety and recyclability standards, addressing the environmental and social impacts of raw material extraction remains a significant challenge. You face issues like resource constraints, as mining lithium, nickel, cobalt, and copper can harm ecosystems and communities. The energy-intensive extraction process also contributes to greenhouse gas emissions. Working conditions in mines often raise ethical concerns, emphasizing the need for transparency and traceability throughout the supply chain. Additionally, environmental pollution and habitat destruction from mining activities worsen ecological damage. To overcome these challenges, you can invest in technological innovations like advanced recycling methods, which recover up to 98% of critical minerals. Promoting sustainable mining practices and improving supply chain transparency are essential steps toward making raw material extraction more sustainable. Implementing traceability systems can help verify the origin of raw materials and ensure ethical sourcing. Incorporating circular economy principles into the supply chain can further reduce reliance on virgin materials and minimize waste.
Industry Collaborations and Initiatives Driving Circular Economy Adoption
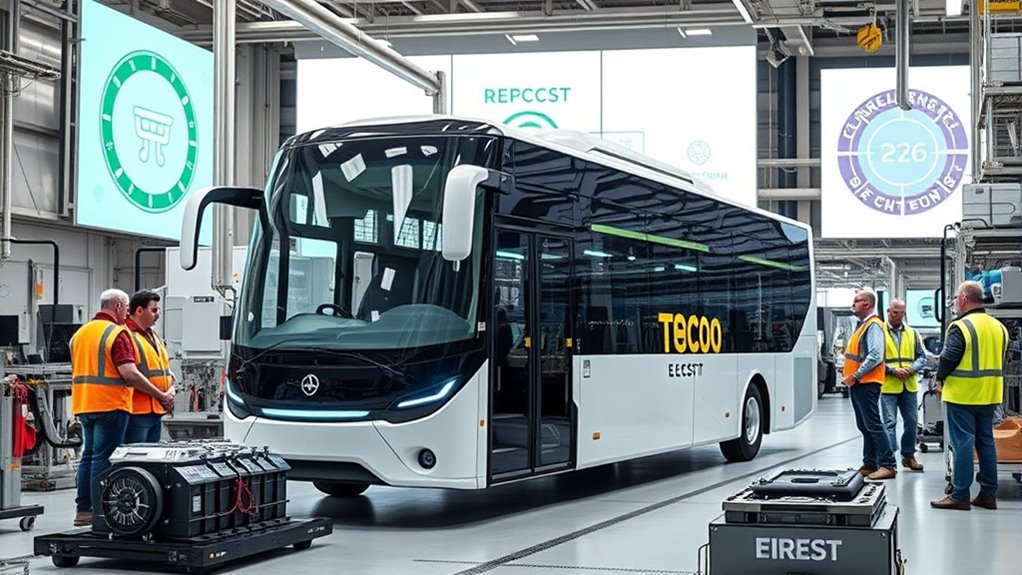
Industry collaborations and initiatives are pivotal in accelerating the adoption of the circular economy in electric bus manufacturing. You’ll see companies like Volvo Buses partnering with recycling firms to repurpose used batteries for energy storage, extending their lifecycle through refurbishment and reuse.
Standards like ISO22628 and policies such as the EU Battery Directive promote recyclability and transparency, ensuring responsible practices.
Educational programs, like WRI’s collaboration with LEGO, teach circular design principles in schools, fostering future innovation.
Cross-sector alliances develop second-life battery applications for grid support, reducing reliance on virgin materials.
Additionally, stakeholder engagement through workshops, industry consortia, and public consultations helps shape best practices and policies.
One key aspect is the Self Watering Plant Pots concept, which exemplifies sustainable design by reducing resource consumption and waste.
These collaborations drive progress, making circular economy goals more achievable and embedded in electric bus manufacturing.
Future Perspectives and Opportunities for Sustainable Electric Bus Manufacturing
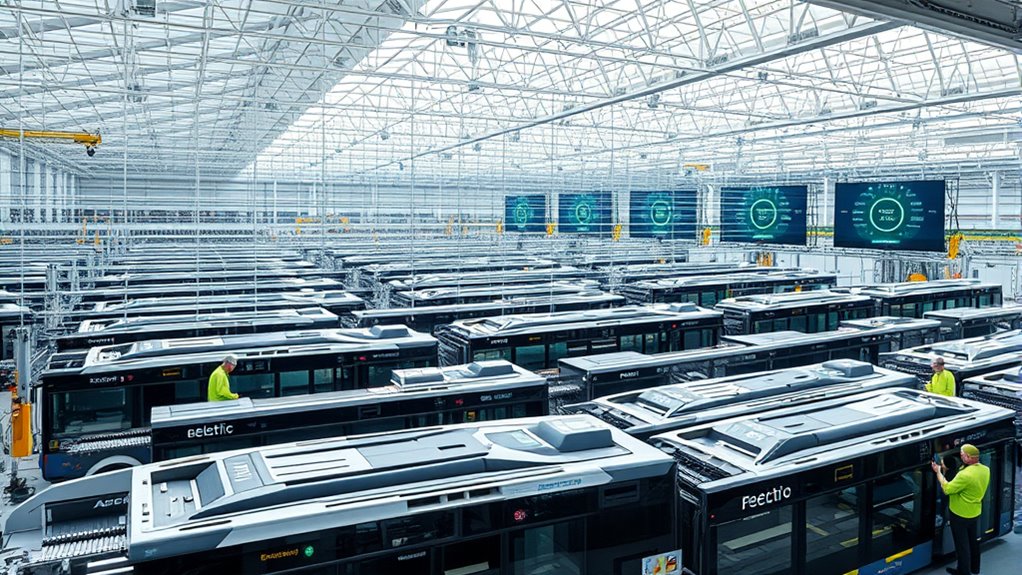
The future of sustainable electric bus manufacturing is promising, driven by significant economic, technological, and environmental opportunities.
You can expect lower fuel costs, saving up to $400,000 per bus over its lifetime, and reduced maintenance expenses. As technology advances, innovations like solid-state batteries, fast-charging systems, and fuel-cell electric buses will boost performance and extend range. These improvements support greener operations, decreasing greenhouse gases and urban air pollution while reducing noise. Additionally, considering cost and budgeting aspects will be essential for the successful adoption and expansion of electric bus fleets. Market forecasts show over 60% of municipal bus sales will be electric by 2030, with battery electric buses dominating. Governments’ incentives and stricter emission regulations further accelerate adoption. Incorporating energy efficiency practices in manufacturing processes can further optimize resource use and reduce environmental impact. Moreover, advancements in battery recycling and the development of green hydrogen will contribute to a circular economy approach, minimizing waste and enhancing sustainability. Additionally, innovations in recycling techniques and the adoption of renewable energy sources will open new avenues for sustainable growth, making electric bus manufacturing more economically viable and environmentally friendly.
Frequently Asked Questions
How Do Manufacturers Ensure Transparency and Accountability in Circular Practices?
You can guarantee transparency and accountability by adopting clear standards and regular reporting on your practices. Use life cycle assessments to evaluate environmental impacts, and involve stakeholders through open communication and public disclosures.
Implement strict auditing and compliance measures, and promote recycling, remanufacturing, and material recovery. Educate consumers and engage communities to build trust.
What Are the Economic Benefits of Adopting Circular Economy Models?
You might think adopting circular economy models costs too much or’s too complex, but the economic benefits are clear. You’ll see reduced material and production costs, boosting profitability.
Plus, you’ll open new markets like refurbished buses and recycled materials, creating fresh revenue streams.
Longer-lasting products mean fewer replacements, saving money over time.
How Do Consumer Behaviors Influence Circularity in Electric Bus Lifecycle Management?
You can influence circularity by making sustainable choices, like buying durable, refurbished, or second-life products. When you support companies that prioritize recycling and reuse, you encourage a shift toward more circular practices.
Your awareness and demand for environmentally friendly options motivate manufacturers to design for disassembly and invest in recycling infrastructure.
What Challenges Exist in Scaling Recycling Infrastructure Globally?
Did you know only 20% of global recycling facilities can handle complex materials like electronics? Scaling recycling infrastructure worldwide faces many hurdles.
You encounter inadequate collection and sorting systems, especially in developing countries. Energy-intensive processes and high operational costs slow progress.
Limited investment and inconsistent regulations also hinder expansion. To overcome these challenges, you need better infrastructure, technology, and international cooperation to create a more sustainable, efficient recycling network globally.
How Will Emerging Technologies Impact Future Battery Reuse and Recycling Methods?
Emerging technologies will transform how you approach battery reuse and recycling. Blockchain enables you to track materials seamlessly, ensuring transparency and compliance.
AI-driven sorting and automation increase recovery rates and efficiency, while digital twins help identify cost-saving opportunities.
Advanced recycling methods like hydrometallurgy and direct recycling preserve valuable materials and reduce energy use.
These innovations will make reuse and recycling more cost-effective, sustainable, and scalable, helping you build a more circular, environmentally friendly battery lifecycle.
Conclusion
Imagine your electric bus as a thriving garden, where every part is reused, recycled, and nurtured to last. By embracing circular practices, you’re not just reducing waste—you’re planting seeds for a sustainable future. Industry efforts show that over 90% of materials can be reclaimed, turning what once was discarded into new growth. Together, you can drive change, ensuring that the journey toward greener transportation becomes a flourishing, shared success.