The water footprint of electric bus manufacturing is considerable, involving water-intensive processes like mineral extraction, metal processing, and assembly. Mining for lithium, cobalt, and copper consumes large water volumes, especially in arid regions, risking local shortages. Manufacturing steps such as smelting and component assembly also use significant water resources, with regional practices and energy sources affecting overall impact. To understand how these factors interact and what can be done to lessen water use, keep exploring further insights.
Key Takeaways
- Electric bus manufacturing involves significant water use in mineral extraction, component fabrication, and assembly processes.
- Critical minerals like lithium, cobalt, and copper require large water volumes, especially in arid extraction regions.
- Regional water availability and efficiency impact the overall water footprint of electric bus production.
- Using renewable energy sources during manufacturing can reduce water consumption and environmental impacts.
- Innovations and sustainable water management practices help minimize water-related ecological risks in production.
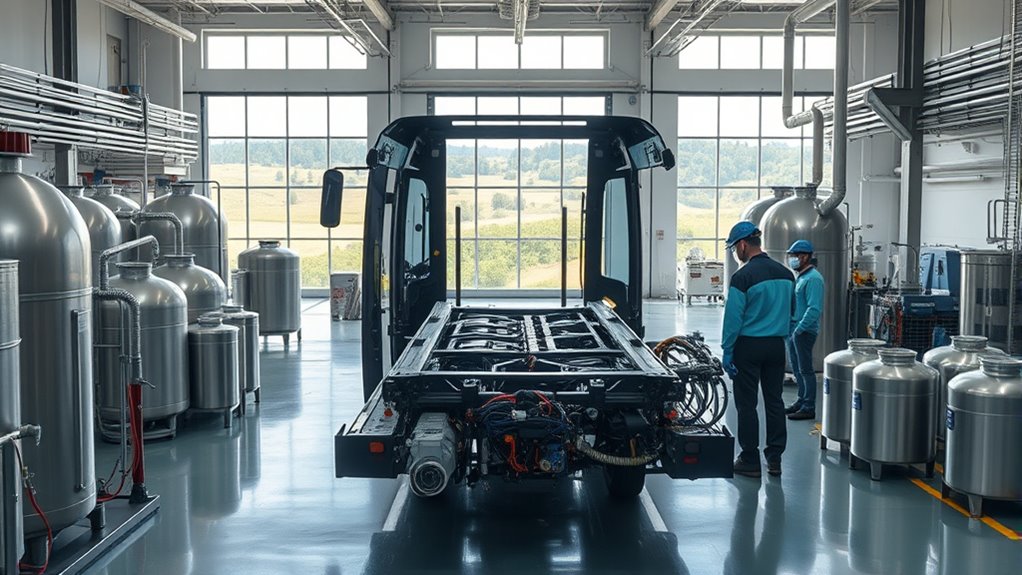
The water footprint of electric bus manufacturing is a critical environmental aspect to contemplate as electric vehicles become more popular. While electric buses are often promoted for their lower emissions during operation, their production demands significant water resources.
This increased water usage stems largely from manufacturing processes like battery production and metal component fabrication. Producing batteries requires the extraction and processing of critical minerals such as lithium, cobalt, and copper, all of which are highly water-intensive activities. Lithium extraction, in particular, consumes large volumes of water, often from arid regions, risking depletion of local water supplies.
Cobalt mining also involves substantial water use, and the environmental risks extend beyond consumption, including potential water pollution from mining runoff.
The manufacturing process itself involves energy-intensive steps such as metal smelting and battery assembly, both of which require large quantities of water. Metal smelting, necessary for producing components like copper wiring, consumes significant water, which can vary depending on the efficiency of the facilities and regional practices.
Additionally, the overall water footprint of electric buses fluctuates based on the regional source of energy used during manufacturing. For example, if the electricity used in production comes from hydropower, the water footprint may be lower, whereas reliance on fossil fuels or thermal power plants can increase water consumption due to cooling needs.
The regional variability in water usage is notable. In areas where mining operations are water-scarce, the environmental impact is more pronounced, risking local water shortages and ecological imbalance.
Moreover, the extraction of minerals carries risks of water pollution, which can harm local ecosystems and communities.
As the demand for electric buses rises globally, understanding the water implications becomes vital. Shifting to renewable energy sources for manufacturing and charging can help mitigate some of these impacts, especially if solar or wind power replaces water-intensive fossil fuel-based electricity.
Efforts to reduce water consumption in manufacturing are ongoing. Improvements in supply chain management, technological advances, and resource recycling can decrease water needs by making processes more efficient and reducing reliance on virgin raw materials.
Implementing sustainable water management practices within manufacturing facilities is essential to minimize environmental risks.
Ultimately, while electric buses offer significant benefits in reducing emissions, mindful consideration of their water footprint during production is necessary to guarantee overall environmental sustainability. Recognizing the regional water resource availability and adapting manufacturing practices accordingly can further enhance sustainability efforts.
Frequently Asked Questions
How Does Electric Bus Water Use Compare to Diesel Bus Manufacturing?
You’re wondering how electric bus water use stacks up against diesel bus manufacturing. Electric buses generally have a higher water footprint because of the water used in mining materials like lithium, cobalt, and copper, as well as electricity generation, especially in water-intensive regions.
In contrast, diesel buses mainly use water during crude oil extraction and refining, which tends to be less water-intensive overall.
What Factors Influence Water Footprint Variations Among Electric Bus Models?
Imagine a fleet of electric buses, each with a different water footprint. You see the impact of material choices, like recycled versus virgin resources, which can cut water use.
You notice manufacturing practices, such as water recycling and energy efficiency, also matter. Additionally, the type of batteries and sourcing strategies create variations.
You realize that smarter supply chains and advanced technology help lower water footprints across different electric bus models.
Are Water-Saving Technologies Being Integrated Into Electric Bus Production?
You might wonder if water-saving technologies are part of electric bus production. While specific integration isn’t widespread yet, there’s a growing trend toward adopting these innovations.
Manufacturers are exploring methods like water reclamation and more efficient processes, often through industry partnerships. Although challenges exist, the move toward sustainable manufacturing means you’ll likely see more water-efficient practices in electric bus production in the future.
How Does Regional Water Scarcity Impact Electric Bus Manufacturing Processes?
You face the challenge of regional water scarcity impacting electric bus manufacturing. Water shortages force you to contemplate relocating facilities, improve water efficiency, and adopt recycling methods.
You must navigate competition with local communities and agriculture, risking delays and higher costs.
You’re also responsible for minimizing environmental harm and supporting sustainable practices while ensuring your production stays resilient amidst climate and infrastructure risks.
What Policies Can Reduce the Water Footprint of Electric Bus Production?
You can reduce the water footprint of electric bus production by implementing water recycling systems and adopting efficient manufacturing technologies.
Setting clear water conservation targets and conducting regular supply chain audits also help identify and improve water use.
Additionally, providing education and training on water-saving practices empowers your team to make sustainable choices, while encouraging sourcing from suppliers with lower water footprints further minimizes overall water use in your production process.
Conclusion
Think of electric bus manufacturing as tending a delicate garden. Every drop of water you invest helps cultivate a cleaner, greener future. Though the process demands care and mindful resource use, your efforts nurture a world where clean transportation blossoms. By understanding and minimizing the water footprint, you become a gardener of change, ensuring that each step taken today blossoms into a sustainable and vibrant tomorrow. Your choices are the seeds of a better future.